Injection Point: Ace & Tate on becoming a Circular business
Ace & Tate is an eyewear brand that offers a wide range of glasses frames, sunglasses, and prescription lenses, with the goal of making quality eyewear accessible to everyone. In addition to offering a range of eyewear products, Ace & Tate is also committed to sustainability. They use eco-friendly materials in their products, and they have a recycling program in place to reduce waste.
The company supplies plastic trial lenses with every pair of glasses sold to protect in order to frame. This creates significant waste, which conflicts with their sustainability goals and B-Corp certification. Consequently, a collaboration was established with Injection Point which is a company that specializes in injection molding (a manufacturing process used to produce plastic parts).
At Injection Point, sustainability is an essential part of their identity. The factory was established and is continuously improved to make plastic injection molding as sustainable as possible. Their goal is to work with companies that consider sustainability essential, want to solve a sustainability issue or strive for more sustainable production.

Ace & Tate fits very well into our portfolio and I see it as a compliment that they come to us because of their sustainability requirements. It is a confirmation of our vision
Cristel Rijnen, Director of Injection Point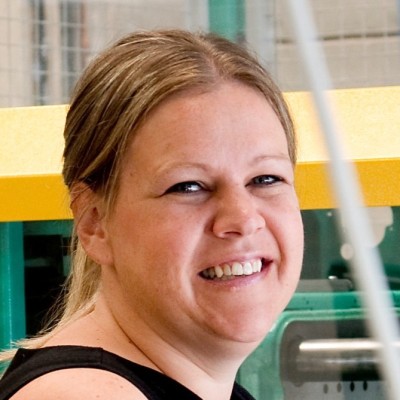
From waste to raw material: the spectacle case from Ace & Tate
In 2017, Ace&Tate discovered that half of its carbon footprint came from packaging. They have scrapped unnecessary packaging to reduce this impact and looked for more sustainable alternatives. As part of their effort to become a circular company, they also wanted to do something with the plastic demo lenses they include with every pair of glasses sold. This is how the idea arose to make spectacle cases from these trial glasses.
After a sustainable audit, they started testing the material, optimizing the product design and designing and developing the mould. As a result, the company has now designed two sizes of glasses cases: one for adults and one for children. The result is eliminating waste from plastic trail lenses, and no new raw materials are needed to produce spectacle cases. Instead, Ace&Tate collects the trial lenses, and reflow processes them into new pellets we use to make the spectacle cases.
Collaborative partneship in the production processes
As a certified B Corp company, Ace & Tate is constantly working on its impact on people and society. The company has set itself the goal of being completely carbon neutral by 2050, which requires significant steps in all areas to reduce CO2 emissions.
On the other side, being in a partnership with a B Corp-certified company means that Injection Point has been audited for its impact on the production process and its ability to meet sustainability requirements. During this audit, they were tested against the Sustainable Development Goals (SDGs), such as being a good employer, sustainability of the factory and materials, and the influence of our factory on the environment.
In practice, this means that the start-up process of their partnership with Ace & Tate was slightly different than usual. Instead of going directly from the question and product drawing to testing and optimizing the design, they first made an intermediate step after it was clear that we could help Ace & Tate with their issue.
Injection point molding with fitting glasses for a circular solution
After agreeing on their sustainable approach, they started testing the material, optimizing the product design and designing as well as developing the mould. The thickness of the spectacle cases varies from thick to thin and closes with a click. For injection molding it is crucial that the mold is filled quickly and completely, otherwise, the product will not come out of the mold correctly. All of the materials used in this process are 100% recycled demo lenses (acrylic plastic). Afterwards it is finished off with an inlay of 50% certified recycled wool felt (GRS certified), 30% wool (R.W.S certified) and lastly 20% polyester. It is an extra challenge when an elongated product has different thicknesses because the plastic must continue to flow evenly until the end of the product.
The glasses case is designed with two parts that click together when the case is closed. It is essential that these parts click together smoothly for a good use, but they should also not be too loose, even after opening and closing hundreds of times. This is a crucial factor in product design and also affects mold design. As a result, the wall thickness of the product is very important in the degree of transparency of the tube. To add the desired color to the base material, advice was given on the amount of dye and natural minerals to achieve the right color intensity, while maintaining transparency.