BioBTX – making circular chemistry possible
BioBTX develops technology to make the transition from a linear fossil world to a circular renewable society possible. The company uses renewable resources such as biomass and plastics to produce drop-in chemicals and aromatics.
BioBTX developed an integrated catalytic pyrolysis process that maximizes BTX yield while minimizes operational costs to enable the production of sustainable and future proof materials.
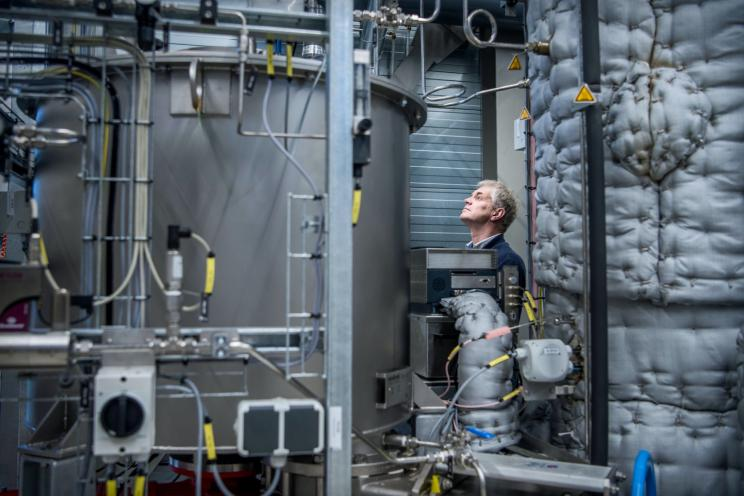
“We see the waste around us - both from plastics and leftover biowaste- as an opportunity to reduce impact on the environment."
BioBTX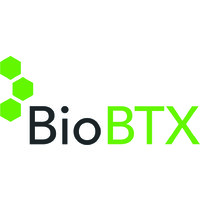
Opening the road for sustainable aromatic mixture
BioBTX started with the goal of developing technology to produce aromatics from non-fossil resources. In the last 10 years the company developed, among others, the world’s first 100% biobased PET, produced BTX out of unsorted plastics and scaled-up the technology with the goal of realizing the world’s first renewable aromatics plant.
The BioBTX Integrated Cascading catalytic Pyrolysis (ICCP) makes it possible to produce high value drop-in chemicals from a wide range of feedstocks. From end-of-life plastics to non-food biomass, the ICCP makes it possible to upcycle a wide range of waste streams.
Without biobased and renewable aromatics the options for sustainable materials are very limited; with these renewable aromatics however, it is possible to achieve truly green and sustainable materials for the entire society and industry.
Data regarding impact
With each kilogram of BTX produced out of plastic waste instead of fossil oil, more than 4 kg of CO2 emissions can be saved. Worldwide more than 150.000.000 tons of BTX is produced every year. Therefore, the BioBTX technology could, when worldwide implemented, lead to 600Mt Of CO2 savings per year. This is approximately 3 times the CO2 capturing of all the trees in the world at this moment every 10 years.